China’s automobile industry development
After years of development, China’s automobile industry has made significant progress in many technologies, especially in recent years, some relatively outstanding domestic engines have emerged one after another. Take the diesel engine as an example, the core components of the engine, and the development of domestic diesel engine technology.
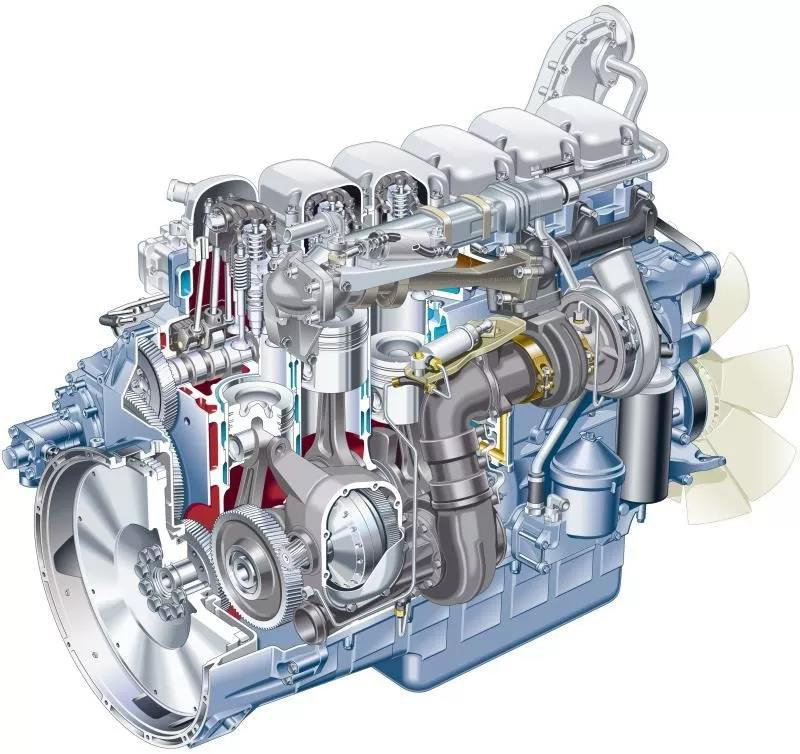
The engine is the heart of the car. It can be said that the engine is one of the most important parts of the car. The composition of the engine is very complex. There are as many as tens of thousands of parts. The engine is a device that converts chemical energy into mechanical energy through combustion. In the final analysis, the key is to achieve efficient combustion by organizing oil and gas to obtain good economy and power, and at the same time to achieve good exhaust emissions through certain means.
Introduction to Fuel System
The key component of the engine responsible for fuel supply is the fuel system, which is also the component with the highest requirements on the matching accuracy of the components.
There are three main types of electronically controlled fuel systems: fuel pumps, electronically controlled unit pumps, and electronically controlled pump nozzles, whose function is to ensure the fuel flow required by the engine under various working conditions and conditions.
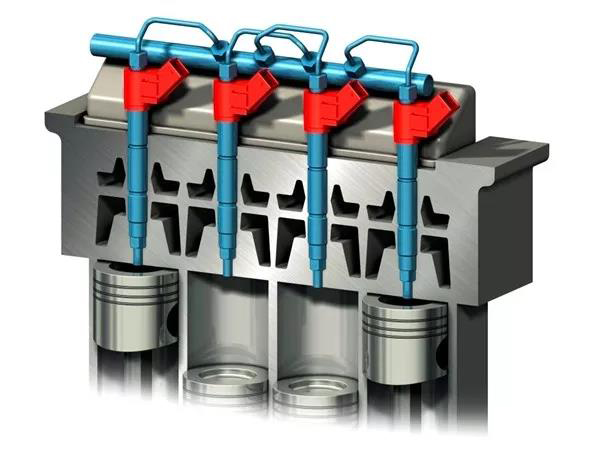
The high-pressure common rail system mainly includes three key components: fuel injection pump, common rail pipe and fuel injector. The technical key lies in: on the one hand, it must achieve precise fuel injection volume control, on the other hand, it must be under extremely high system pressure. Ensure reliability.
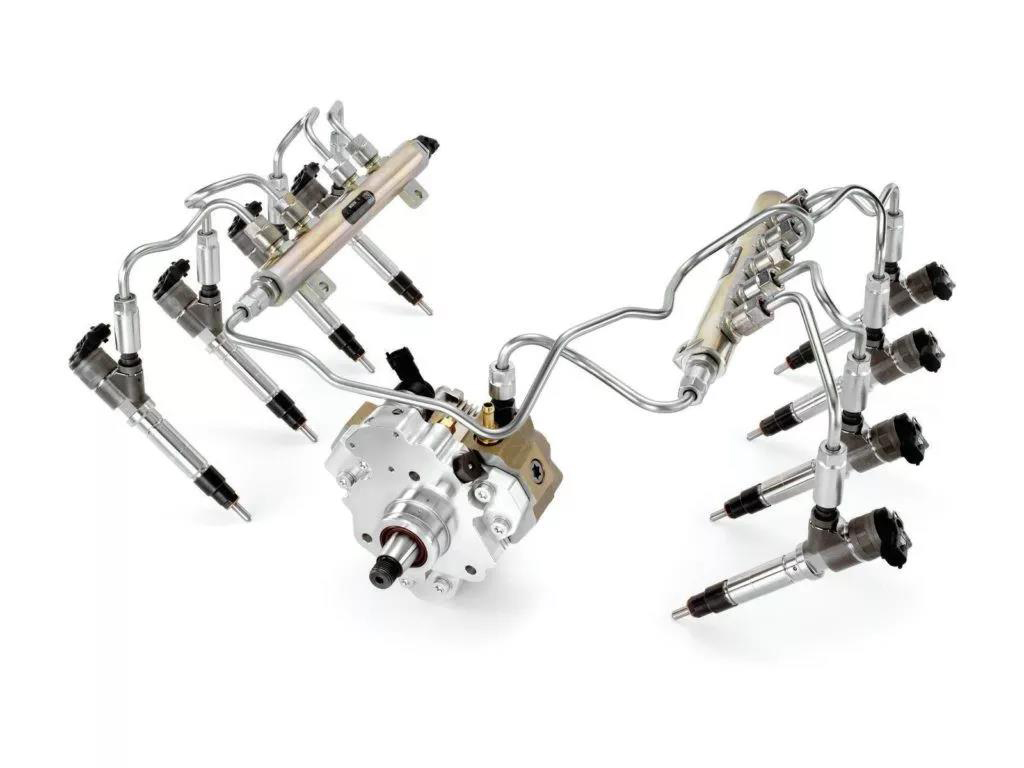
Most of the current diesel engines use electronic control injection systems. Compared with traditional mechanical injection systems, electronic control injection systems can effectively improve the power and economy of diesel engines, and at the same time greatly reduce exhaust pollution. Today we will briefly talk about the working principle and composition of the diesel electronically controlled injection system.
Due to the combustion characteristics of diesel engines, the fuel supply system of diesel engines has its own unique fuel injection rules: if the initial fuel injection rate is high, the work will be rough and the noise will be loud; if the later fuel injection rate is small, the supplementary combustion will increase, and the economy will be poor; If the average fuel injection rate is small (the fuel injection time is long), the combustion speed is slow, and the power and economy are poor. Therefore, the ideal fuel injection rule: first delay and then urgently, and shorten the fuel injection time as much as possible. In this way, the traditional mechanical fuel supply method has been difficult to meet the fuel injection rules of diesel engines. Therefore, electronically controlled diesel injection systems have emerged.
Performance requirements
The combustion process requires the fuel system to achieve multiple fuel injections, including pre-injection, main injection, and post-injection. Pre-injection is to reduce noise, post-injection is to increase exhaust temperature to meet emission requirements, and main injection is for combustion work. Pre-injection and post-injection spray each time the oil volume is very small, reaching the level of 1mg. In order to meet this requirement, the matching clearance between the needle valve of the injector and the needle valve body is at the level of 1μm. At present, the new products of domestic diesel engines are mostly 5 injections, including 2 pre-injections, 1 main injection, and 2 post-injections. The most advanced fuel system in the world can achieve up to 8 injections, including 3 pre-injections, 1 main injection and 4 post-injections.
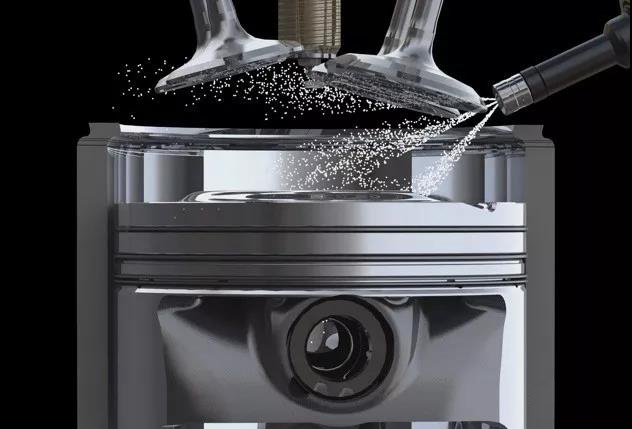
For example, the rated speed of a 4-stroke diesel engine is 3000 rpm, corresponding to 1500 combustions per cylinder per minute, and the 8-shot fuel system can achieve 12,000 injections per minute. In order to achieve such a high frequency of injection times and high-precision injection oil volume, it is first necessary to fit a precision pair with a very small clearance, then the parts need to have high wear resistance, and finally it is necessary to increase the injection pressure to shorten the injection cycle.
The rail pressure of the fuel system is getting higher and higher with technological progress. At present, the rail pressure of new domestic diesel engine products is mostly around 1800 bar, while the rail pressure in the world is relatively high.
The rail pressure for the advanced fuel system has reached 2500bar. This is 2500 atmospheres. Under such high pressure, the parts are durable and reliable.
At the same time, there is no fuel leakage, and very stringent requirements are put forward on the parts materials, processing technology, and sealing structure.
Supplier situation
Chinese fuel system suppliers have made great progress in recent years. Enterprises have achieved independent design and production by digesting and absorbing foreign patented technologies and introducing foreign advanced equipment. Some have developed high-pressure fuel systems up to 2000bar. However, because the product’s performance, consistency and reliability have not been fully verified, it has not been fully recognized by the vehicle manufacturer. It is believed that with the increase of supporting application products, China’s production of fuel systems will occupy a broader market with advantageous prices in the future.