The common rail injection system of diesel engines has a common feature, that is, there is a common high-pressure fuel accumulator, called common rail. The high-pressure fuel supply pump is only responsible for supplying high-pressure fuel to this accumulator, and is not responsible for controlling fuel quantitative and injection timing. The task of managing fuel pressure and delivering fuel to each cylinder is accomplished through a common rail. In this way, the fuel injection process can be free from pressure generation and fuel delivery process; fuel quantitative control and fuel injection timing control can be more flexible and free.
Compared with other fuel injection systems, the common rail fuel injection system has the following characteristics: full electronic and flexible control of fuel quantitative and fuel injection timing; fuel injection rule curve shape can be adjusted relatively freely; optimized and reachable 1800bar fuel injection pressure (second only to Bosch’s pump nozzle and pump nozzle) control; can achieve up to seven fuel injections per working cycle; high compactness and low high-pressure fuel pump drive torque.
ECD-U2 Common Rail Fuel Injection System of Denso Corporation
Denso took the lead in introducing a common rail fuel injection system called ECD-U2 in the early 1990s. The ECD-U2 common rail fuel injection system consists of a high-pressure fuel supply pump, common rail, fuel injectors, electronic control units and various sensors that control these components. The system uses the pump control valve to change the fuel output of the high-pressure fuel supply pump to control the common rail pressure. The common rail pressure is adjusted according to the value determined by the engine load and speed. The pump control valve is combined with the fuel pressure sensor to perform closed-loop control of the common rail pressure.
The working principle of the injector
The common rail pressure has been applied to the bottom surface of the injector needle valve for a long time. It is applied to the back of the needle valve only when the injector is not energized. When the fuel injector is not energized, the three-way valve connects the cavity above the one-way orifice with the common rail. High-pressure fuel flows into the control chamber (above the hydraulic plunger) through the one-way orifice, and the needle valve is directed by the hydraulic plunger. Applying downward pressure, together with the force of the return spring, overcomes the fuel pressure under the needle valve and closes the needle valve. In this process, the one-way orifice plate has no throttling effect.
When the ECU sends out a fuel injection pulse, the three-way valve connects the cavity above the one-way orifice with the return pipe, and the fuel flows to the return pipe. The pressure of the high-pressure fuel filled in this cavity immediately drops to atmospheric pressure. Due to the one-way orifice throttling, the pressure in the control chamber below it can only drop slowly, and the injector needle valve gradually rises, resulting in the so-called delta (triangular) fuel injection pattern. This fuel injection pattern It is very beneficial to the combustion in the cylinder.
When the fuel injection duration controlled by the electronic control unit elapses, the fuel injector is de-energized and the three-way valve returns to its initial state. At this time, the high-pressure fuel from the common rail flows into the control chamber through the three-way valve and the one-way orifice, so that the control chamber quickly reaches the common rail pressure, the needle valve is quickly closed, and the fuel injection is quickly cut off.
It can be seen that the opening and closing of the fuel injector is completely determined by the difference between the pressure in the control cavity of the fuel injector and the common rail pressure. Changing the width of the electrical pulse applied to the three-way valve can control the amount of fuel injection; changing the time when the electrical pulse applied to the three-way valve occurs can control the timing of fuel injection. Because the ECD-U2 common rail injection system is a fully electronically controlled, complete pressure-time fuel quantitative control system, it does not have the inherent problems of traditional fuel injection systems, such as: difficult to control due to pressure propagation in the fuel injection system Or uncontrollable operating conditions; poor control efficiency at low speeds caused by insufficient governor control capabilities.
Three shapes of fuel injection pattern
The fuel injection pattern of ECD-U2 common rail injection system can be controlled into three shapes, namely delta type (triangular type), shoe type and pre-injection type:
• Delta type (triangular type) injection rate type: a type in which the injection rate gradually rises and ends quickly
• Pre-injection type: a type of pre-injection with a small amount of oil before the main injection
• Boot-shaped fuel injection rate pattern: the pre-spray and the main spray are connected together to form a boot-shaped fuel injection rate pattern
One of the most significant is the pre-spray. Pre-injection is to provide a small pre-injection pulse before the main injection pulse, so the three-way valve is opened twice in each injection. The amount of pre-spray is as small as 1 cubic millimeter/stroke. The interval between pre-spray and main spray can be reduced to 0.1 milliseconds. Pre-injection can reduce the combustible mixture formed during the stagnation period, thereby effectively reducing the combustion noise of the diesel engine.
The control strategy of the high-pressure fuel supply pump
The function of the high-pressure fuel supply pump is to control the oil output to produce high-pressure fuel. It uses a cam drive mechanism that is easy to generate high pressure. The lift equivalent of the plunger after the pump control valve is closed determines the oil output. By controlling the closing time of the pump control valve or controlling the cam pre-lift to control the oil output, the fuel is returned and quantified without being compressed, thereby reducing high-pressure oil return. Therefore, the pump drive torque is significantly reduced. The maximum drive torque is only one third of the inline pump.
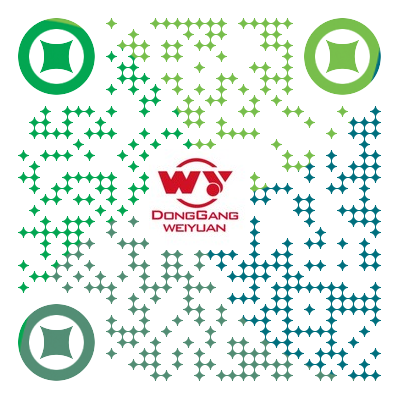