As a leader in the non-road engine industry, Caterpillar has begun to launch engines that meet the fourth stage in recent years. Today I want to introduce to you the engine of the 349F excavator C13. I believe that many maintenance personnel have seen this engine, and today we will introduce the engine’s fuel system in detail.
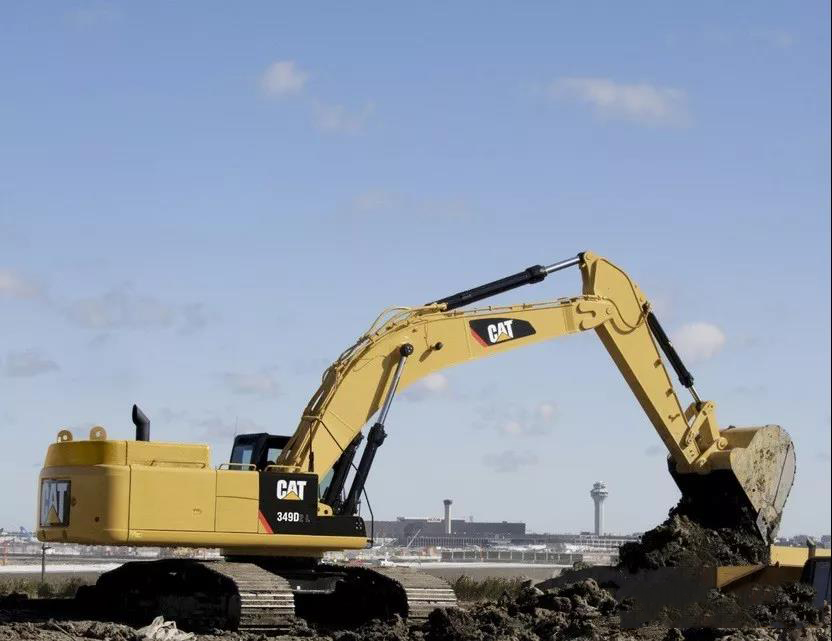
Fuel system layout
First, I present the system layout diagram of the engine fuel system as follows:

(1) Secondary fuel filter base with two 4 micron fuel filters
(2) Oil supply common rail in cylinder head
(3) Double valve electronically controlled pump nozzle (EUI)
(4) Return pressure regulator
(5) The fuel flow from the electric priming pump to the ARD through the 1900 kPa regulator
(6) Shunt actuator
(7) Electric charge pump
(8) Primary fuel filter base
(9) Fuel tank
(10) 1900 kPa fuel regulator
(11) Primary fuel filter with oil-water separator
(12) Fuel transfer pump
(13) Speed sensor
(14) Pressure sensor
(15) Battery
(16) Temperature sensor
(17) Timing calibration connector
(18) Throttle position sensor
(19) Oil level sensor
(20) SAE J1939 data link
(21) Electronic Control Module (ECM)
(22) Alarm indicator
(23) Diagnostic indicator
(24) Programmable output
(25) PTO SET/RESUME (set/restore) switch
(26) Power output (PTO) on/off switch
(27) Key switch
The electronic unit injector system includes the following systems: mechanical system and electronic system. The mechanical system includes a low-pressure fuel supply system and a mechanical and electronic unit injector. The electronic system can provide a complete set of all engine electronic control functions. The electronic control system consists of the following three components: input, control and output.
The electronically controlled pump nozzle fuel system has six main components:
1.Mechatronics unit injector
2.Fuel transfer pump
3.ECM
4.sensor
5.The electromagnetic valve
6.Camshaft
The fuel injection pressure generated by the electronically controlled pump nozzle is as high as 207000 kPa (30000 psi), and it will fire up to 19 times per second at the rated speed. The fuel transfer pump draws fuel from the fuel tank and uses the internal fuel pressure regulator to pressurize the system to 60 and 125 psi to supply fuel to the fuel injector. The ECM provides precise control to the injector solenoid valve to achieve engine performance and meet emission standards. The sensor is an electronic device used to monitor the performance parameters of the engine. Engine performance parameters are used to measure pressure, temperature and speed. This information will be sent to the ECM via a signal. Solenoid valves are electronic devices that can use the current sent by the ECM to change the performance of the engine. The injector solenoid valve is one such solenoid valve.
Low pressure fuel oil circuit
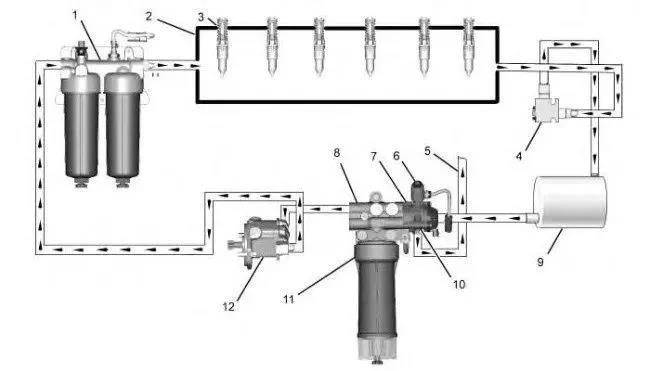
(1) Fuel fine filter
(2) Common rail in cylinder head
(3) Double valve electric control pump nozzle
(4) Return pressure regulator
(5) The fuel flow from the electric priming pump to the ARD through the 1900 kPa regulator
(6) Shunt actuator
(7) Electric charge pump
(8) Primary fuel filter base
(9) Fuel tank
(10) 1900 kPa fuel regulator
(11) Primary fuel filter and oil-water separator
(12) Fuel transfer pump
The low-pressure fuel system supplies fuel from the fuel tank to the fuel injectors.
The low pressure fuel system has four basic functions:
Provide fuel needed for combustion
Provide fuel to cool the injector.
Remove the air from the fuel.
Preheat the fuel in the fuel tank.
The low pressure fuel system includes the following main components:
Fuel tank
Fuel oil pipeline
Primary fuel filter or oil-water separator
Fuel transfer pump
Fuel fine filter
Fuel injection pump
Fuel pressure regulator for ARD and engine fuel supply.
Return pressure regulator
Mechatronic unit injectors, fuel delivery pumps, ECMs, sensors and solenoid valves are all part of the low-pressure fuel system.
In the low-pressure fuel system, the fuel is drawn from the fuel tank and sent to the primary fuel filter or the oil-water separator. Before the fuel flows into the fuel transfer pump (12), the primary fuel filter (11) removes debris larger than 10 microns from the fuel. The fuel transfer pump is a gear pump with a pressure relief valve inside. The pressure relief valve will open at approximately 60 to 125 PSI. The fuel flows from the outlet of the fuel delivery pump to the secondary fuel filter. The 4 micron filter removes small abrasive impurities from the fuel system, which can damage the unit injector.
The primary fuel filter base (8) contains an electric priming pump (7). The electric charge pump forces the air out of the system through the orifice on the regulator. Fuel filling is usually performed after repairing the fuel system (for example, replacing the fuel filter). When air is mixed in the fuel filter, fuel line, and other fuel system components, the engine may be difficult to start. This fault can also occur when the engine has not been operated for a long time. When there is air in the fuel line, the electric charge pump can be started by turning the switch or turning the start switch to charge the system. The length of time to fill the fuel system depends on the specifications of the system, the length of the fuel pipe and the size of the filter. The time required to fill the fuel system is approximately 30 seconds. This value varies with different applications.
The primary fuel filter base also contains a one-way valve to prevent backflow of fuel during filling.
The return pressure regulator (4) consists of a spring-loaded check valve. When the engine is in the off position and the fuel pressure drops below 60 PSI, the check valve is closed. The check valve is closed to prevent the fuel in the cylinder head from flowing back to the fuel tank. The fuel remaining in the cylinder head maintains the fuel supply of the injector during the start.
The ECM controls the main functions of the engine. The sensor is an electronic device used to monitor the performance parameters of the engine. The pressure sensor, temperature sensor and speed sensor all provide information to the ECM through a voltage signal. Actuators are electronic devices that can use the current sent by the ECM to change the performance of the engine. The injector solenoid valve is an actuator.
Electronic control device
The electronic control system can provide a complete set of all engine electronic control functions. The electronic control system consists of the following three components: input, control and output. The sensor monitors the running status of the engine. This information will be sent to ECM. ECM has three main functions. The ECM will provide power to the engine electrical equipment and monitor the input signal of the engine sensor. ECM is also used as a governor to control engine speed. The ECM stores current faults, recorded faults and recorded events. The personality module is the software in the ECM, which includes specific operating conditions diagrams that limit power, torque, and engine speed. The ECM supplies current to the output components to control the engine operation. The ECM has the following components: two 70-pin harness connectors, an engine harness connector and a vehicle harness connector. The vehicle wiring harness is used to connect the ECM to the engine control part of the vehicle wiring harness.
The engine control part includes the following components:
Gearbox
brake
Clutch switch
PTO switch
Data link
Check engine indicator
Alarm indicator
Engine retarder switch
Tachometer
Tachometer
Cooling fan solenoid valve
The features in the following list are part of the electronic control system:
Cold start measures
hydraulics pressure
Coolant temperature alarm indicator
Automatic altitude compensation
Variable injection timing
Engine electronic speed control
These characteristics can have the following effects:
Precise engine speed control, very small amount of smoke, faster cold start and built-in engine protection.
ECM consists of the following two main components:
ECM and personality modules.
The ECM is a computer, and the personality module is the computer’s software. The personality module contains a graph of the engine’s operating conditions.
The working condition diagram determines the following characteristics of the engine:
power
Torque curve
Rotating speed
Other features
The ECM, personality modules, sensors and unit injectors cooperate with each other to control the engine. The ECM, personality modules, sensors and unit injectors cannot control the engine alone.
ECM determines the ideal speed based on the following criteria:
Throttle signal
Certain diagnostic codes
Speed signal
The ECM senses the actual engine speed to maintain the ideal engine speed. The ECM calculates the amount of fuel required to reach the desired speed.
Electronically controlled pump nozzle mechanism
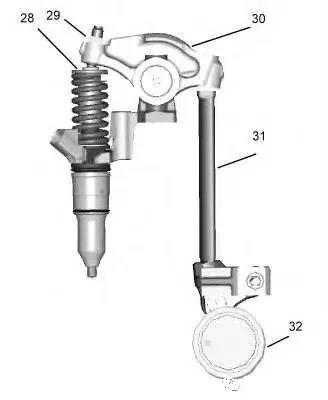
(28) Double valve electric control pump nozzle
(29) Adjusting nut
(30) Rocker arm assembly
(31) Putter
(32) Camshaft
The electronically controlled pump nozzle (28) pressurizes the fuel. Then, the correct amount of fuel is injected into the cylinder at the precise moment. ECM can determine the timing of fuel injection and the amount of fuel injected into the cylinder. The nozzle of the electronically controlled pump is operated by a camshaft cam and a rocker arm. There are three camshaft cams on the camshaft for each cylinder. Among them, two cams manipulate the intake and exhaust valves, and the other cam manipulates the unit injector mechanism. The thrust is sent from the pump nozzle cam on the camshaft (32) to the push rod (31) through the tappet. The thrust of the push rod is sent to the top of the pump nozzle through the rocker arm assembly (30). The transmitted thrust pushes down the plunger in the top of the injector. The movement of the plunger injects fuel into the cylinder. The adjusting nut (29) is used to adjust the nozzle of the electronically controlled pump.
Double valve electric control pump nozzle
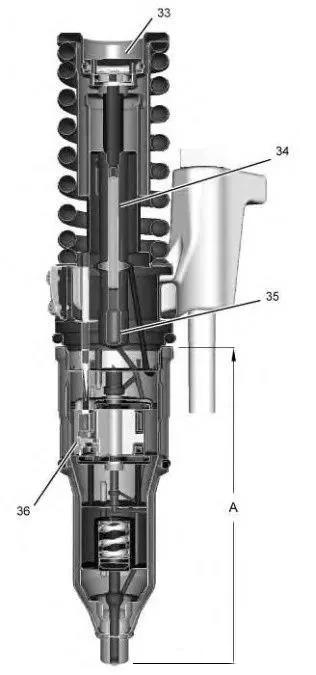
(33) Tappet
(34) Plunger
(35) Plunger sleeve
(36) Solenoid valve
(A) Nozzle assembly
Injection timing and fuel delivery
The ECM controls the fuel injection volume by changing the signal sent to the pump nozzle. The pump nozzle will only inject fuel when the solenoid valve (36) is energized. The ECM sends a voltage signal to the solenoid valve to energize the solenoid valve. The ECM controls the injection timing by controlling the timing of this 90 V signal. The ECM controls the fuel injection volume by controlling the duration of this voltage signal.
The fuel injection timing is determined by the engine speed and other engine data. The ECM can sense the position of the top dead center of the No. 1 cylinder through the signal provided by the engine speed sensor. The ECM determines when the fuel should be injected relative to the top dead center position. The ECM will send a signal to the nozzle of the electronically controlled pump when needed.
The above is the content shared today. If you need a product, you can also find it on the official website or the mall linked below. Your attention is the biggest motivation for my creation, thank you.
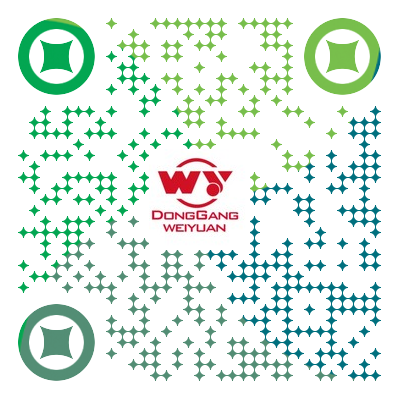