Precautions for disassembly and assembly of CP2.2
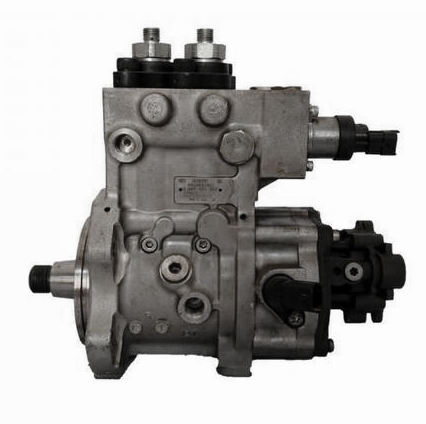
Try to use a suction device for cleaning
The color of the seal ring of the sub-cylinder element: the upper part, red; the lower part, gray
Each sub-cylinder should be marked before disassembly, and the box where each sub-cylinder component is placed should be marked accordingly
The relationship between the oil inlet of the sub-cylinder and the oil inlet of the master cylinder to supply oil to the sub-cylinder: same side
Installation gap of speed phase sensor: 0.8~1.2mm
Tightening torque requirements:
Inlet oil metering proportional valve: 6~7Nm
Fastening screw of sub-cylinder: 35~45Nm
Drive end bearing cap screw: 16~20Nm
Fastening screw of gear pump speed increasing ring gear: 190~210Nm
Fastening screw of speed sensor: 7~9Nm
Gear pump fastening screw: 7~9Nm
Screw for blocking process hole of roller body retainer: 12~15Nm
Precautions for disassembly and assembly of CP3.3
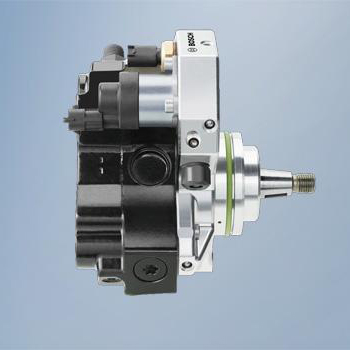
Each sub-cylinder should be marked before disassembly, and the box where each sub-cylinder component is placed should be marked accordingly
When removing the bearing flange, use your fingers to hold the drive shaft to avoid pulling out the drive shaft at the same time
Tightening method of bearing flange fastening screws:
Light yellow or black: 12~14Nm tighten and loosen, 11~13Nm tighten
Silver gray: 14~16Nm tighten and loosen, 14~16Nm tighten
Inlet oil metering proportional valve: 6~7Nm
Tightening method of gear pump fastening screw:
Light yellow or black: 3~5Nm pre-tightened and loosened, 7~9Nm tightened
Silver gray: 8~10Nm tighten and loosen, 8~10Nm tighten
Oil inlet screw joint
Light yellow or black:
M6×1, 7.5~8.5Nm tighten;
M12×1.5, 23~27Nm tighten, loosen, 28~32Nm tighten
Silver gray: M6×1, 7.5~8.5Nm tighten;