Integrated fuel supply module
Dear colleagues in the fuel system maintenance industry, many people are consulting the assembly on how to check and repair Cummins HPI injectors and the corresponding fuel system. After doing a lot of research and practical work, here is the relevant content for everyone, I believe it will help you to serve this fuel system well.
HPI (High pressure Injection) high pressure fuel injection system is a fuel supply system developed by Cummins and Scania for heavy-duty diesel engines. The system uses mechanical fuel injectors and is equipped with an electronic management system. The fuel injection pressure is 2500bar. It is widely used in Cummins heavy/super heavy diesel engines ranging from 15 liters to 78 liters.
This system uses Cummins’ typical Time-Pressure control mode diesel fuel injector, and the fuel nozzle is an open fuel nozzle (will be introduced in a separate article).
The system uses an external metering fuel control valve and timing fuel control valve to control the right amount of fuel to enter the injector. The metering fuel control valve controls the amount of fuel injected by the injector, and the timing fuel control valve controls the injection. Oil start and end time.
The structure of HPI-TP system is as follows:
In order to better understand the working principle of the HPI fuel system, we will introduce the working principle of the system and common troubleshooting methods in detail several times.
This article is the first part: I will introduce the main components and working principle of HPI-TP oil supply system. The following figure shows the layout of the hydraulic circuit.
(one) Fuel from the fuel tank (1)First, it flows through a coarse filter (150 microns) equipped with an oil-water separator. Then the fuel flows into the IFSM, which is the Integrated Fuel System Module (Integrated Fuel System Module).
(two) The incoming oil flows through the electronic fuel supply pump (2) .
The electronic fuel supply pump will work within 2 minutes after the engine is started. In order to ensure that fuel is supplied from the fuel tank to the fuel pump as soon as possible, and to improve the starting performance of the engine.
(three) After passing the electronic fuel pump, there is an electronic fuel pump bypass valve (21) with a pressure of 0.07 kg,The function of the bypass valve is to expel the air in the oil circuit as soon as possible, so as to improve the engine starting performance.
(four) When the engine is started,A gear-type fuel pump (4) will be able to autonomously suck fuel from the fuel tank into the pump through an anti-reverse suction check valve (20). The fuel supply of the electronic fuel supply pump is no longer needed, and the electronic fuel supply pump stops working two minutes after the engine is started.
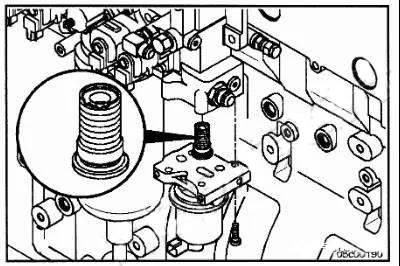
(five) Fuel pump (4) The gear pump will provide sufficient flow and stable pressure fuel for the entire fuel system.
(six) Between the gear pump and the diesel fine filter, a 26 kg pressure limiting valve (18) is equipped. This valve functions as a safety valve. If there is any blockage in the oil circuit behind the gear pump, this valve will Open, the fuel will flow back to the fuel tank through the fuel return channel.
(seven) After passing through the pressure limiting valve (18), the fuel will flow through a 15-micron diesel fine filter (6) with a filtration efficiency of 98%.
(eight ) The fuel flows to the fuel cutoff valve (7) after passing through the diesel fine filter (6). This valve is controlled by the computer board. When the engine has an extreme operating failure, it will cut off the fuel supply to the injector, making the engine Downtime. The picture below shows the position of the oil shutoff valve:
(nine ) After that, the fuel will flow to a 17.2 kg fuel constant pressure valve (9) to limit and maintain the fuel system pressure. The excess fuel will open the valve and flow to the cooling plate (10) where the computer board is located. The plate is cooled, and then flows back to the fuel inlet of the fuel pump. The flow of the fuel circuit accounts for about 35% of the output fuel supply of the fuel pump.
(ten) The fuel supply pressure is stable. The computer board will control the amount of fuel flowing to the injector by controlling the opening time of the four solenoid valves. Each control valve is normally closed. When the solenoid valve receives the control current from the computer board, it will open the oil circuit so that the fuel can enter the metered fuel oil passage and the timing fuel oil passage.
(eleven) Injectors are divided into two groups, front-end injector group (1/2/3 cylinder) and back-end injector group (4/5/6 cylinder);
Each group has three injectors, and each group of injectors will be controlled by a metering fuel control valve (12) and a timing fuel control valve (13).
Since the firing sequence of each cylinder is 1/5/3/6/2/4, with the cam position of each cylinder, it can be ensured that only one injector is in a position that can receive metered fuel and timing fuel entry.
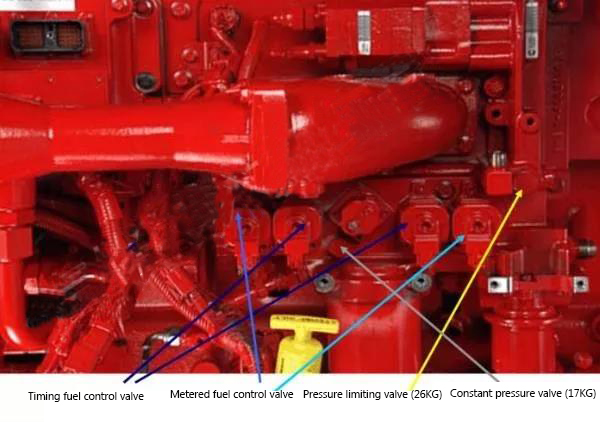

(twelve ) Subsequently, the fuel will be distributed through the internal pipeline to the metering inlet and timing inlet of each injector at the front/rear end.
When the fuel injector metering process and timing process are completed, the cam drives the upper plunger of the fuel injector to go down, and a hydraulic link is formed inside the fuel injector, and the internal pressure rises to start fuel injection. The fuel injection will end after the lower plunger of the fuel injector reaches the sealing seat surface of the fuel nozzle.
Due to the special design of the nozzle, the end of the injection process of the HPI-TP injector will be very fast.
The fuel above the injector timing plunger will flow out of the injector and flow into the cylinder head after the injector completes the injection, and then flows back into the oil return passage of the integrated fuel control module, and finally returns to the fuel tank.
The specific structure and working principle of the fuel injector will be described in detail in a later article.
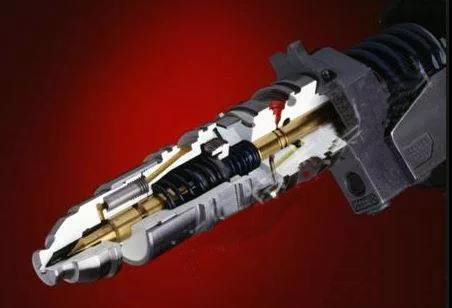
(thirteen) When the engine is stopped, the fuel between the normally closed metering fuel control valve (12) and the fuel injector will be trapped and cannot flow out.
These fuels in a closed state will absorb the heat of the engine. When the fuel temperature rises, its volume will also expand and cause the pressure in the metered fuel passage to rise.
This will cause the start resistance of the starter motor to rise and cause difficulty in starting the engine hot.
In order to solve this problem, a very small orifice (0.008 inch) is designed on the metering fuel oil passage and a check valve is designed on the metering flow control valve to release the pressure rise caused by high temperature.
The above is an introduction to the oil circuit components and working principle of the Cummins HPI-TP fuel system.