What is high pressure common rail?
High-pressure common rail technology refers to a fuel supply method that completely separates the generation of injection pressure and the injection process in a closed-loop system composed of high-pressure fuel pumps, pressure sensors and ECUs. The high-pressure fuel pump delivers high-pressure fuel to the public fuel supply. Through precise control of the oil pressure in the common oil supply pipe, the pressure of the high-pressure oil pipe has nothing to do with the engine speed, which can greatly reduce the change of the diesel engine oil supply pressure with the engine speed, thus reducing the defects of the traditional diesel engine. . The ECU controls the fuel injection volume of the fuel injector. The fuel injection volume depends on the pressure of the fuel rail (common fuel supply pipe) and the opening time of the solenoid valve.
What is the use of high pressure common rail?
The high-pressure fuel pump delivers the fuel to the public fuel supply pipe, and directly injects the fuel into the cylinder by controlling the fuel injector. The high-pressure common rail completely separates the injection process and the generation of oil pressure, so that the oil supply pressure will not be affected by the engine speed.
advantage:
1. The injection pressure in the high-pressure common rail system is flexibly adjustable, and the optimal injection pressure can be determined for different working conditions, thereby optimizing the overall performance of the diesel engine.
2. It can independently and flexibly control the fuel injection timing, and with high injection pressure (120MPa~200MPa), it can simultaneously control NOx and particulate (PM) within a small value to meet emission requirements.
3. Flexible control of fuel injection rate changes to achieve ideal fuel injection rules, easy to achieve pre-injection and multiple injections, which can not only reduce diesel engine NOx, but also ensure excellent power and economy.
4. The fuel injection is controlled by the solenoid valve. The control accuracy is high. There will be no bubbles and zero residual pressure in the high-pressure oil circuit. Therefore, within the operating range of the diesel engine, the circulating fuel injection volume changes little and the fuel supply of each cylinder is uneven It can be improved to reduce diesel engine vibration and reduce emissions.
1. What is the performance of unplugging the fuel metering unit?
All the fuel enters the common rail pipe, causing the rail pressure to be too high, the pressure limiting valve opens, and the limp mode is entered. It is also easy to cause the oil temperature to rise, which is not good for the whole system. Frequent opening of the PRV valve will affect the life of the system. You need to plug in the fuel metering unit and start the car again.
2. In the limp mode, what does the accelerator pedal do?
The accelerator pedal works, but the power cannot be pulled up, and the speed can only reach 1500 rpm.
3. What are the maximum, minimum and normal values of inlet pressure and temperature after the intercooler?
The pressure and temperature after intercooling are closely related to engine emissions and performance. For specific values, please refer to the test data of the bench test in the technical center laboratory. Generally speaking, under rated conditions, the pressure and temperature after intercooling are 110kPa and 360Ps for intercooling. Back pressure 160kPa, temperature 55±5℃
4. What is the density of the gas before and after the intercooler?
We generally only pay attention to pressure, temperature, volume, PR/V=constant, this is a general equation.
5. What are the maximum, minimum and normal values of oil pressure and temperature?
Oil pressure range during normal operation (when oil temperature ≥80℃)… 100~600kPa
The instantaneous oil pressure peak value when the diesel engine starts….1000kPa
Minimum oil pressure for normal operation
Rated working condition …………380kPa
Maximum torque working condition …250kPa
Idling conditions …… 100kPa
Oil pressure alarm value…………60kPa
The maximum allowable temperature of the main oil channel oil …… 100℃
The maximum allowable temperature of the oil in the oil pool ………120℃
6. What are the maximum, minimum, and normal values of water temperature?
The normal value of water temperature is 80-95 degrees, 85 degrees is the temperature that the driver can easily accept
Allowable maximum temperature of diesel engine coolant outlet (alarm temperature) ….. 96℃
Recommended minimum temperature of diesel engine coolant outlet …… 60℃
The maximum allowable coolant temperature in a short time ……105℃
7. What are the oil requirements for engine oil and diesel?
Diesel engine lubricating oil grade (GB11122-1997) CF grade
Fuel brand (GB252-2000)
Does Euro III have special requirements for diesel? (Yes, mainly several indicators, such as sulfur content, polycyclic aromatic hydrocarbons and other factors that affect emissions. For details, see the emission standard GB17951-2005)
8. What are the principles and detection standards of all sensors?
testing method:
First check for open circuit, then check for short circuit;
Check the resistance value (what is the resistance value?)
These have special documents. The OEMs should not pay attention to the sensors on the diesel engines. We will inspect them by ourselves. The OEM puts its energy on several of its own sensors. Such as vehicle speed, switch signals, etc.
9. What is the injector control strategy?
Duty cycle output
10. Principle of synchronization signal
Explain according to the picture. Generally do not talk about this thing, it is easy to talk about dizziness, simply mention: judge the ignition position (crankshaft position, judge cylinder)
11. Can the oil pump provide pressure? Is there a check valve in the low pressure oil circuit?
Less than 9 bar absolute pressure (Euro III); there is a one-way valve in the hand oil pump.
12. What is the injection hole diameter of the injector?
Roughly within 20 silk (Less than 0.2mm). We judge the injector from the flow rate, such as 860ml/30sec. Spray 860ml diesel at a certain rail pressure for 30 seconds.
13. How much water temperature can you start (starting when the temperature is too low, it is easy to cause pulling of the cylinder?
Generally, users are required to run at idle speed for 2-3 minutes after starting the engine, and the oil pressure should be higher than 100kPa. When the water temperature is not higher than 60℃, do not run at high speed and heavy load suddenly. When the water temperature is too high, the heat dissipation capacity is lacking, and it is easy to pull the cylinder.
14. What is the intake air volume of the air filter? What is the limit value?
The driver feels weak to refuel, he will think of replacement when he smokes, or have an experienced kilometer. It is rarely tested. WeChat and Chetong connect Shenzhen to get more maintenance sharing information.
There are two concepts here, one is the actual intake air volume of the air filter, which is the air intake volume of the engine, and the other is the rated intake air volume of the air filter. Generally, the rated air intake volume will be greater than the actual air intake volume. The recommended air filter The rated flow of… ≥1400 m3/h When the air filter resistance is greater than 6kPa, the air filter element should be cleaned or replaced.
15. Are there positive and negative signs on the fuel injector terminal?
no
16. What is the difference in inlet pressure of the intercooler?
Normal 4-7KP. The pressure drop of the intercooler should not be greater than 12kPa
17. What is the reason for piston burning?
It is generally believed that it is caused by poor atomization of the injector, abnormal combustion on the top surface of the piston, and the gradual development of high temperature on the top surface of the piston.
18. What is the oil consumption?
Ratio of oil to diesel consumption: 4:1000
The ratio of MAN is: 10:1000
The national standard stipulates that the ratio of oil to diesel consumption of vehicle diesel engines under rated operating conditions shall not exceed 0.2%.
The oil consumption at Euro III will affect particulate emissions.
19. After stopping, what is the loop of high pressure oil in the common rail pipe?
Usually leaked from the injector
20. Will the battery loss affect the work of ECU?
The normal working range of ECU is 6V-32V. The starter is the most affected by the battery loss, which will cause the starter to not work normally.
21. What is the speed of the starter when it starts?
200r/min
22. If all 6 cylinders of the engine are leaking, can KTS detect it?
If a cylinder leaks, it can be tested by compression test.
Judge the air leakage of 6 cylinders by comparing with the speed of other engines
23. Is there an automatic oil cut-off function for high-pressure oil pipe fracture?
No. (Nippon Denso’s Euro III engine has installed a floating ball valve joint between the common rail pipe and the high-pressure oil outlet pipe to prevent fuel loss when the high-pressure oil pipe suddenly breaks. WeChat search car connects Shenzhen. During normal operation, The oil pressure on both sides of the ball valve is the same, and the ball valve floats in the middle of the joint; when the high-pressure oil pipe suddenly breaks, the high-pressure oil will press the ball valve on the side of the broken joint of the oil pipe, blocking the oil outlet.)
24. Is the power of the exhaust brake valve electricity or compressed gas?
compressed gas
25. Are the dual brakes installed on the same gas path? Is it a pneumatic switch? (Some cars have brakes on the front and rear wheels)
Mechanical switch installed on the same gas path
26. Where are the clutch switches and brake switches installed?
Under the clutch and brake switch
27. Does the exhaust brake do much damage to the supercharger and engine?
Normal use does not cause much damage to the supercharger and engine
28. The cooling oil circuit of ECU is a straight pipe, is the cooling effect obvious?
Due to the continuous flow of fuel, the temperature is lower and the cooling effect is obvious.
Representative models:
At the end of 1999, the Smart equipped with a 3-cylinder common rail diesel engine was born. Its displacement is only 799mL, the maximum power is 30kW, and the maximum torque is 100Nm at 1800-2800rpm.
Mercedes-Benz’s E320 is equipped with a second-generation common rail engine. The output torque is 250Nm at a maximum power of 150kW/1000rpm, 85% of the peak torque can be obtained at 1400rpm, and a peak torque of 500Nm can be achieved in a wide area of 1800-2600rpm. The acceleration time from 0 to 100km/h is only 7.7 seconds, and the maximum speed is 243km/h. The comprehensive fuel consumption is 6.9L/100km, and the 80L fuel tank makes the endurance reach 1000km. The combined fuel consumption of the E320 equipped with a gasoline engine is 9.9L/100km.
Technical summary:
In a diesel engine, the high-speed operation makes the diesel injection process only a few thousandths of a second. Experiments have shown that the pressure of the high-pressure fuel pipe varies with time and position during the injection process. Due to the compressibility of diesel fuel and the pressure fluctuation of diesel fuel in the high-pressure fuel pipe, the actual fuel injection state is quite different from the plunger fuel supply rule specified by the fuel injection pump. The pressure fluctuation in the oil pipe sometimes causes the pressure in the high-pressure oil pipe to rise again after the main injection, reaching the pressure to open the needle valve of the injector, and reopen the closed needle valve to produce a secondary injection phenomenon. Since the secondary fuel injection cannot be completely burned, the smoke and hydrocarbon (HC) emissions are increased, and fuel consumption increases. In addition, the residual pressure in the high-pressure oil pipe will change after each injection cycle, which will cause unstable injection, especially in the low-speed area. The above phenomenon is easy to occur. In severe cases, not only the injection is uneven, but also intermittent non-injection phenomenon. In order to solve the defect of diesel engine fuel pressure changes, modern diesel engines use a technology called common rail.
High-pressure common rail technology refers to a fuel supply method that completely separates the generation of injection pressure and the injection process in a closed-loop system composed of high-pressure fuel pumps, pressure sensors and ECUs. The high-pressure fuel pumps deliver high-pressure fuel to the public fuel supply pipe. Through the precise control of the oil pressure in the public oil supply pipe, the pressure of the high-pressure oil pipe has nothing to do with the engine speed, which can greatly reduce the change of the diesel engine oil supply pressure with the engine speed, thus reducing the defects of the traditional diesel engine. The ECU controls the fuel injection volume of the fuel injector. The fuel injection volume depends on the pressure of the fuel rail (common fuel supply pipe) and the opening time of the solenoid valve.
Technical principle:
The high-pressure common rail system is mainly composed of an electronic control unit, a high-pressure oil pump, a pressure accumulator (common rail pipe), an electronic control injector, and various sensors. The low-pressure fuel pump feeds fuel into the high-pressure fuel pump, and the high-pressure fuel pump pressurizes the fuel into the high-pressure fuel rail (accumulator). The pressure in the high-pressure fuel rail is adjusted by the electronic control unit according to the fuel rail pressure measured by the fuel rail pressure sensor and needs to be adjusted , The fuel in the high-pressure fuel rail passes through the high-pressure fuel pipe. According to the operating state of the machine, the electronic control unit determines the appropriate fuel injection timing and the fuel injection duration. The electronic fuel injector is controlled by the electro-hydraulic to inject the fuel into the cylinder.
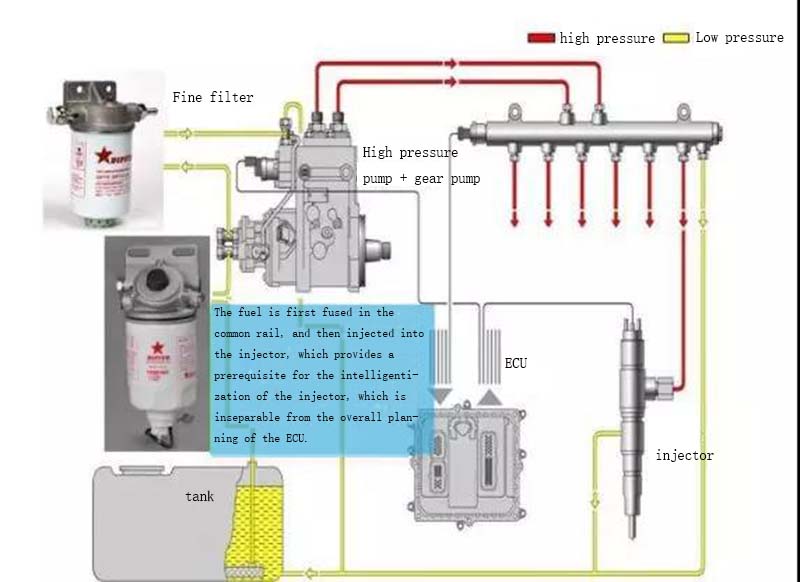
1. High pressure oil pump
The design criteria for the fuel supply volume of the high-pressure fuel pump is to ensure the sum of the fuel injection volume and the control fuel volume of the diesel engine under any circumstances, as well as the fuel volume changes during starting and acceleration. Since the injection pressure in the common rail system is independent of the fuel injection process, and the injection timing is not guaranteed by the cam of the high-pressure fuel pump, the pressure cam of the high-pressure fuel pump can have the lowest peak torque, the lowest contact stress and the most wear-resistant The design principle to design the cam.
Most companies use a three-cylinder radial piston pump driven by a diesel engine to generate pressures up to 135MPa. The high-pressure oil pump uses multiple oil-pressure cams in each oil-pressure unit, so that its peak torque is reduced to 1/9 of that of the traditional high-pressure oil pump, the load is also relatively uniform, and the operating noise is reduced. The pressure control in the high-pressure common rail cavity in this system is achieved by draining the fuel in the common rail cavity. In order to reduce power loss, the three-cylinder radial plunger will be closed when the fuel injection volume is small. An oil pressure unit in the pump reduces the oil supply.
2. High pressure fuel rail (common rail pipe)
The common rail pipe distributes the high-pressure fuel provided by the fuel supply pump to the fuel injectors, acting as a pressure accumulator. Its volume should reduce the fuel supply pressure fluctuations of the high-pressure fuel pump and the pressure fluctuations of each injector caused by the fuel injection process, so that the pressure fluctuations in the high-pressure fuel rail should be controlled below 5MPa. However, its volume cannot be too large to ensure that the common rail has sufficient pressure response speed to quickly track changes in diesel engine operating conditions.
Pressure sensors, flow buffers (flow restrictors) and pressure limiters are also installed on the high-pressure common rail pipe. The pressure sensor provides the pressure signal of the high-pressure fuel rail to the ECU; the fluid flow buffer (flow limiter) ensures that the fuel supply to the fuel injector is cut off when the fuel leak occurs in the fuel injector, and can reduce the common rail and the high-pressure fuel pipe. Pressure fluctuations; the pressure limiter ensures that the pressure in the high-pressure fuel rail is quickly discharged when the pressure of the high-pressure fuel rail is abnormal.
image
3. Electronically controlled fuel injector
The electronic control injector is the most critical and complex component in the common rail fuel system. Its function is based on the control signal sent by the ECU and controls the opening and closing of the solenoid valve to optimize the fuel in the high-pressure fuel rail. The fuel injection timing, fuel injection quantity and fuel injection rate are injected into the combustion chamber of the diesel engine.
In order to achieve the predetermined fuel injection shape, a reasonable optimization design of the fuel injector is required. The volume of the control room determines the sensitivity of the needle valve when it is opened. The volume of the control room is too large, and the needle valve cannot achieve rapid fuel cut at the end of fuel injection, which makes the later fuel atomization poor; the volume of the control room is too small, Can not provide enough effective stroke for the needle valve to increase the flow resistance of the injection process, so the volume of the control room should also be reasonably selected according to the maximum fuel injection volume of the model.
In addition, the minimum fuel injection pressure of the fuel injection nozzle depends on the flow rate of the oil return orifice and the oil intake and the end surface area of the control piston. In this way, after determining the structural dimensions of the fuel inlet, return, and control chamber, the stable and shortest fuel injection process for the full opening of the needle valve of the fuel injector is determined, and the stable minimum fuel injection process of the fuel injector is determined at the same time. The amount of oil. The reduction of the volume of the control chamber can make the response speed of the needle valve faster, so that the fuel temperature has a smaller effect on the injection volume of the nozzle.
However, the volume of the control room cannot be reduced indefinitely. It should be able to ensure the lift of the needle valve of the fuel injector so that the needle valve is fully opened. The two control orifices determine the dynamic pressure in the control chamber, thereby determining the movement law of the needle valve. By carefully adjusting the flow coefficients of these two orifices, an ideal fuel injection law can be produced.
Because the injection pressure of the high-pressure common rail injection system is very high, the cross-sectional area of the nozzle hole of its nozzle is very small. For example, the nozzle hole diameter of BOSCH company’s nozzle is 0.169mm×6. Under such a high injection pressure, the fuel flow is extremely unstable, the spray cone angle of the fuel beam becomes larger, and the fuel atomization is better, but the penetration distance becomes smaller. Therefore, the vortex intensity and combustion chamber structure of the original diesel engine should be changed. Shape to ensure the best combustion process.
For the injector solenoid valve, since the common rail system requires it to have a sufficient opening speed, considering that pre-injection is an important injection method to improve the performance of the diesel engine, the response time of the control solenoid valve should be shortened.
image
4. High-pressure tubing
The high-pressure fuel pipe is the channel connecting the common rail pipe and the electronic control injector. It should have enough fuel flow to reduce the pressure drop when the fuel is flowing, and make the pressure fluctuation in the high-pressure pipeline system small, and can withstand the high-pressure fuel Impact action, and the pressure in the common rail can be quickly built up when starting. The length of the high-pressure oil pipes of each cylinder should be as equal as possible, so that each injector of the diesel engine has the same fuel injection pressure, thereby reducing the deviation of the fuel injection volume between the engine’s cylinders. Each high-pressure oil pipe should be as short as possible to minimize the pressure loss from the common rail to the fuel injection nozzle. The outer diameter of BOSCH’s high-pressure oil pipe is 6mm and the inner diameter is 2.4mm, and the outer diameter of the high-pressure oil pipe of Denso Corporation is 8mm and the inner diameter is 3mm.
The high pressure in the common rail cavity is directly used for injection, which can eliminate the pressure boosting mechanism in the injector; and the common rail cavity is continuously high pressure, and the driving torque required by the high pressure oil pump is much smaller than that of the traditional oil pump.
Through the pressure adjustment solenoid valve on the high-pressure oil pump, the oil pressure in the common rail cavity can be flexibly adjusted according to the engine load condition and the requirements of economy and emission, especially the low-speed performance of the engine is optimized.
The solenoid valve on the injector controls the injection timing, injection volume and injection rate, and can flexibly adjust the injection volume of the pre-injection and post-injection and the interval with the main injection under different working conditions.
The high-pressure common rail system is composed of five parts, namely, high-pressure oil pump, common-rail cavity and high-pressure oil pipe, fuel injector, electronic control unit, various sensors and actuators. The fuel supply pump pumps fuel from the fuel tank to the inlet of the high-pressure fuel pump. The high-pressure fuel pump driven by the engine pressurizes the fuel and sends it into the common rail cavity. Then solenoid valves control the injectors of each cylinder to inject fuel at the corresponding time.
Pre-injection before the main injection, injects a small part of the fuel into the cylinder, pre-mixing or partial combustion occurs in the cylinder, shortening the ignition delay period of the main injection. In this way, both the rate of increase in cylinder pressure and the peak pressure will decrease, the engine will work more moderately, and the decrease in cylinder temperature will reduce NOx emissions. Pre-injection can also reduce the possibility of misfire and improve the cold start performance of the high-pressure common rail system.
Decreasing the injection rate at the beginning of the main injection can also reduce the amount of fuel injected into the cylinder during the ignition delay period. Increasing the injection rate in the middle of the main injection can shorten the injection time and shorten the retarding period, so that the combustion is completed within the more effective crank angle range of the engine, and the output power is increased, fuel consumption is reduced, and soot emissions are reduced. The rapid fuel cut off at the end of the main injection can reduce incompletely burned fuel and reduce smoke and hydrocarbon emissions.
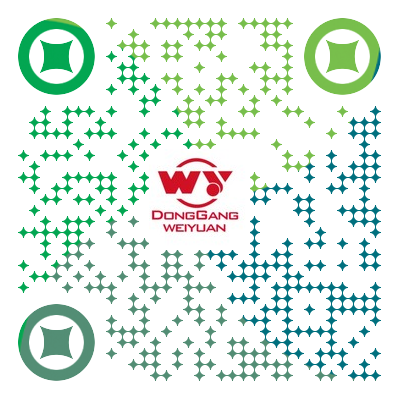